‘Botox of plastic’ to freeze power costs
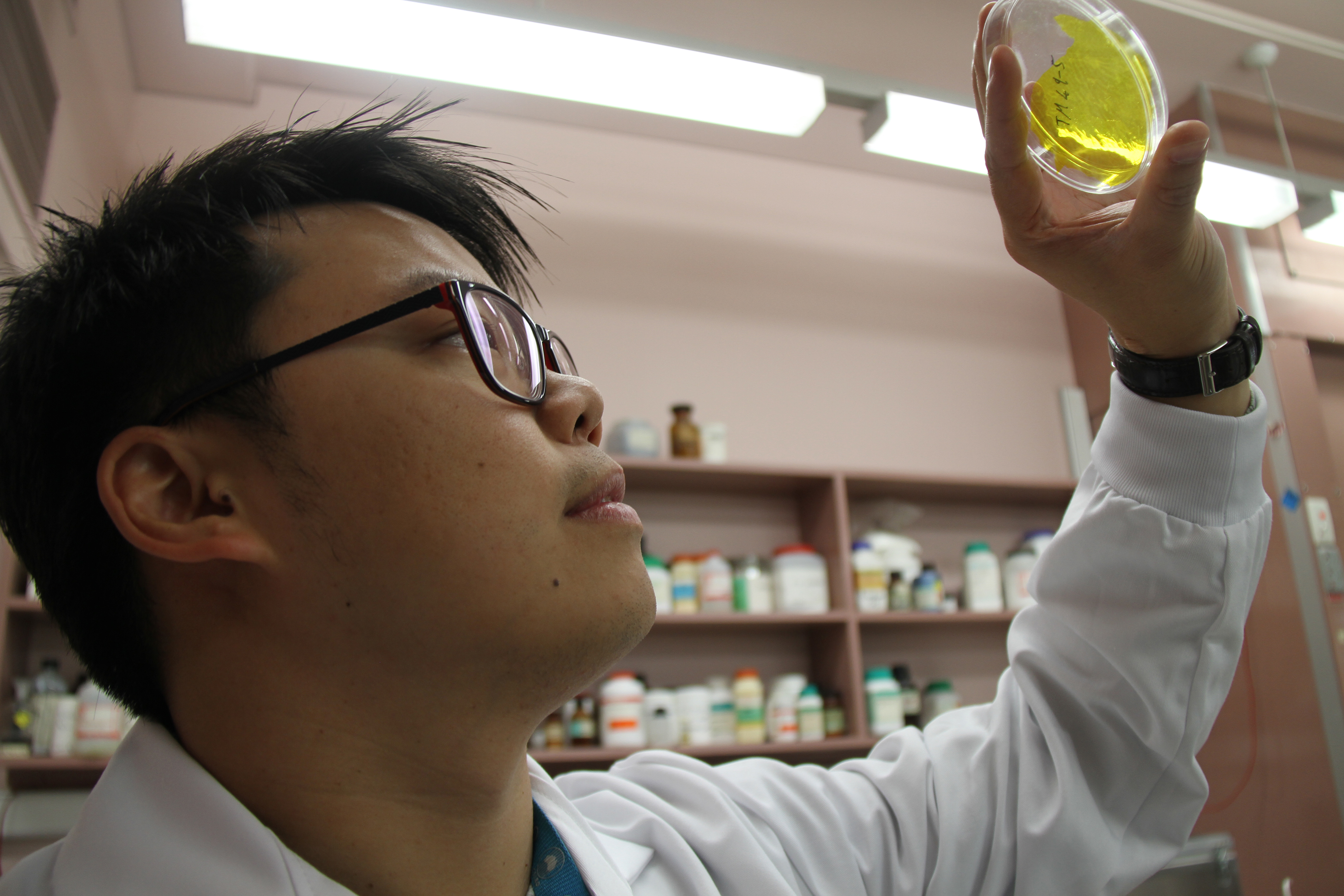
A new material that prevents plastic from ageing has been developed by CSIRO – offering huge environmental and cost savings for the energy industry.
When applied to plastic lining this ‘botox for plastic’ can clean up exhaust gases from power plants much more effectively than existing methods.
Currently, the techniques industry use to separate out raw materials such as gases, liquids and solids are extremely energy-intensive, accounting for 40 per cent of the world’s energy use each year.
According to lead author Dr Sam Lau, the new ‘botox’ technique offers a solution that will make the separation process a staggering 50 times faster.
“At the moment power generators rely on plastic linings made up of tiny holes just one nanometre wide, a tiny fraction of a width of a human hair,” he said.
“For decades scientists have been trying to improve the efficiency of this process by using plastics with larger holes. However, these larger openings tend to age very quickly and collapse within a matter of days.
“What we’ve done is make use of incredible compact materials known as Metallic Organic Frameworks – or MOFs – which have the surface area of a football field in just one gram.
“We found that the density of the MOFs acts like a shot of botox and actually freezes the larger holey structures in place for an entire year.”
This suddenly makes the lining with larger holes a viable option for industry, allowing them to complete separation processes at 50 times the speed.
“This is a much more environmentally friendly approach and of course translates into huge cost and efficiency savings for the companies who take this up,” Dr Lau said.
According to Dr Lau, not only does the technique have incredible potential for cleaning up exhaust gases from power plants, it could also be used to enhance the purity of natural gas streams, the separation of water from alcohols (a key process in biofuel synthesis) and for dye removal in the textile industry.
“We’re extremely excited by this discovery and hope to see it being applied commercially within one to two years,” he said.